Introduction: CNC Processing of Advanced Ceramics
CNC machining of ceramics refers to the use of Computer Numerical Control (CNC) machines to perform precision processes such as milling, drilling, and grinding on ceramic materials.The entire machining process is controlled by computer programs, allowing for the precise manufacturing of complex shapes and meeting the micron-level accuracy requirements.
Challenges in Machining Ceramic Materials
Most advanced ceramics possess exceptional hardness and a relatively high level of brittleness, surpassing that of metals.These material properties pose significant challenges in the CNC machining process:
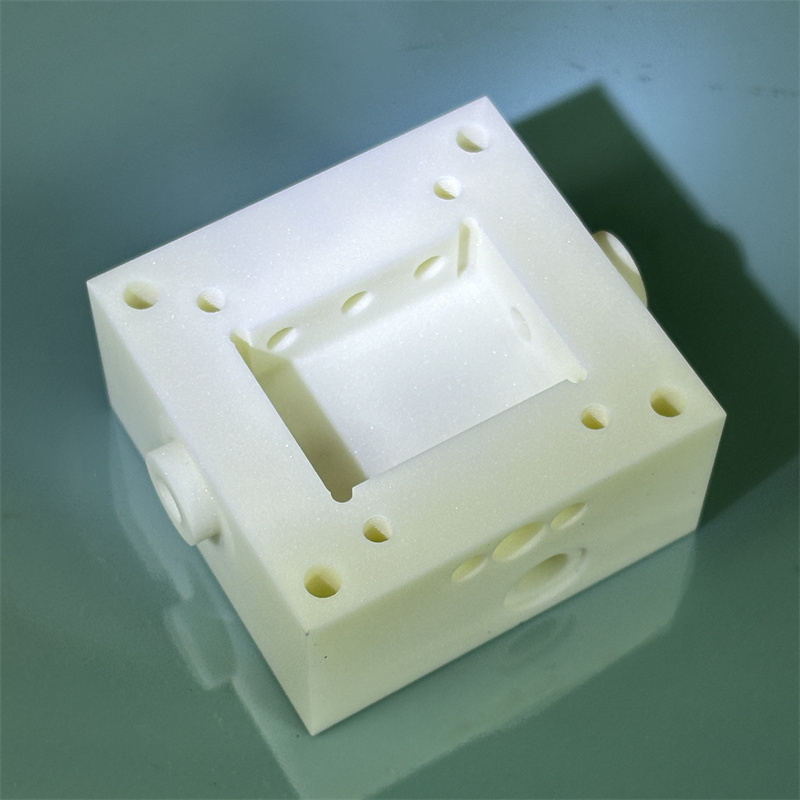
· The machining of ceramic components typically involves grinding, which is a time-consuming process. Due to the brittleness of ceramic materials, CNC machining of alumina ceramics is prone to chipping. Therefore, CNC equipment used for machining technical ceramics generally requires tools made of higher-hardness non-metallic materials.
· The characteristics of ceramic materials impose higher demands on the experience and expertise of machinists. Skilled machinists need to have a solid understanding of mechanics, perform precise calculations of stress distribution and force transmission for ceramic components prior to CNC machining, and carefully design the feed rate and mechanical balance of the equipment.
· For high-precision and complex geometries in ceramic components, CNC machining requires not only the proper setting of basic cutting parameters (such as feed rate, spindle speed, and cutting depth) but also the programming of complex tool paths, multiple finishing passes, and tool compensation. Additionally, real-time measurement of machining errors, feedback, and adjustments are necessary to ensure the final machining accuracy.
Advantages of CNC Machining Advanced Ceramics
· Micron-level machining precision.
· Accurate quality control.
· Capability to achieve customized complex shapes and small holes through CNC machining.
· Precise control of machining paths to minimize material waste.
Our CNC Machining Capabilities
· Advanced five-axis CNC equipment and precision grinding machines for complex structural components.
· CAM software programming.
· Skilled CNC technicians with years of machining experience.
Precision Tolerances in Technical Ceramics Machining
· Minimum part size: 1 mm
· Maximum dimensions: 650 mm (L) × 1500 mm (W) × 60 mm (Th)
What is the minimum tolerance we can achieve? Precision and tolerance standards for advanced ceramics.</a >
Advanced Ceramic Tolerance and Precision Standards Table |
|||
Tolerance Type |
Specific Tolerance |
Reference Standards |
MIN Tolerance We Can |
Geometric Tolerance |
Flatness |
ISO 1101 / |
2μm(Within 300 mm) |
|
Straightness |
ISO 1101 / |
2μm(Within 100 mm) |
|
Cylindricity |
ISO 12181 / |
2 μm |
|
Concentricity |
ISO 1101 / |
5 μm |
|
Perpendicularity |
ISO 1101 / |
2 μm(Within 100 mm) |
|
Parallelism |
ISO 1101 / |
2 μm(Within 300 mm) |
|
Symmetry |
ISO 1101 / |
5 μm |
|
True Position |
ISO 1101 / |
1 μm (Within 300 mm) |
|
Surface Profile |
ISO 1101 / |
3 μm (Within 200 mm) |
|
Total Runout |
ISO 1101 / |
5 μm |
|
Angular Tolerances |
ISO 2768 / |
± 0.05° |
|
|
|
|
Surface Quality |
Surface Roughness |
ISO 4287 / |
Ra 0.019 μm |
Why Choose WEIERT ?
- R&D Support: We offer end-to-end services, from raw material formulation (customizing chemical compositions) to precision machining, tailored to your specific needs.
- Quality Management: Certified with ISO 9001, we integrate Kazuo Inamori’s management philosophy into our CNC machining services to ensure excellence in every aspect.
Advanced Ceramic Manufacturer in China
WEIERT CERAMICS’ advanced ceramic materials with reference to international and Chinese advanced ceramics standards, ensuring superior quality. Our quality is guided by ISO/TC 206, ASTM C28, CEN/TC 184, and Chinese GB/T and JC/T standards to meet the needs of high-end applications. Contact us for more information!