Cerámica de magnesia(MgO)
Qué es el magnesioa (MgO) ¿Cerámica?
El óxido de magnesio (MgO) es un compuesto ampliamente utilizado, derivado principalmente de la magnesita (aproximadamente 93%), con una porción más pequeña obtenida de salmueras y depósitos de sal profundos (alrededor de 7%). El proceso de producción suele consistir en la calcinación para formar periclasa, seguida de la fusión en horno de arco eléctrico. El material resultante se tritura y se muele selectivamente hasta obtener el tamaño de partícula deseado, y puede seguir transformándose en productos de diversas formas y estructuras porosas, según las necesidades.
El MgO puede clasificarse en tres tipos en función de las materias primas y los métodos de producción. Entre ellos, la FM (magnesia fundida) y la DBM (magnesia calcinada a muerte) son los tipos más utilizados en la producción de componentes cerámicos de alta temperatura, como piezas aislantes, crisoles y revestimientos de hornos.
Las cerámicas de MgO combinan las características de los materiales refractarios tradicionales con las de las cerámicas avanzadas. Ofrecen resistencia a la corrosión por metales alcalinos y mantienen la estabilidad química y frente a las radiaciones, lo que las hace adecuadas para su uso en energía nuclear y procesos de alta temperatura en metalurgia. La temperatura máxima teórica de trabajo es de hasta 2200°C, con un uso continuo en el rango de 1600-1800°C. Sin embargo, las cerámicas de MgO tienen algunas limitaciones, como una resistencia al choque térmico relativamente baja y una alta reactividad química. Tienden a reaccionar con el oxígeno, el nitrógeno y el vapor de agua, y su aplicación en vacío requiere un control estricto de la presión y la selección de gases inertes.
Artículo | CCM (Magnesia calcinada cáustica) |
DBM (Magnesia quemada muerta) |
FM (Magnesia fundida) |
Industria de aplicación | Cloruro de magnesio, magnesia marina | Industria de materiales refractarios | Industria de materiales refractarios |
Materia prima Fuente |
Cloruro de magnesio/Magnesia de agua de mar | Magnesita | MgO de grano fino y denso de gran pureza (99,83%) |
Usos típicos | Fertilizantes, piensos, tratamiento de aguas residuales | Refractarios conformados/no conformados: Ladrillos de MgO-C, ladrillos de MgO-Al, mezcla de gunitado, arcilla de piqueras, etc. | Refractarios de alto rendimiento: alto horno, revestimiento de hornos eléctricos, revestimiento de cucharas de colada, hornos de alta temperatura; cerámica especial, desulfurizador, soporte de catalizador |
Escenarios de aplicación | Uso general de productos químicos industriales | Se utiliza como revestimiento de hornos en las industrias del acero, la energía y el vidrio. | Escenarios que requieren una mayor resistencia a la corrosión y resistencia a altas temperaturas |
Ejemplos de industrias | Agricultura, Protección del medio ambiente | Acero, energía, vidrio | Aeroespacial, Transición energética, Infraestructuras, Refino de metales |
Características | Alta actividad, buena reactividad | Rentable para escenarios de demanda económica | Alta pureza, alta densidad, resistencia superior a la corrosión y a las altas temperaturas |
Mezcla de ingredientes y modificaciones:
Durante la preparación, la composición del MgO se ajusta cuidadosamente. Para mejorar la sinterización, aumentar ligeramente el tamaño del grano y reducir la tendencia a la hidratación, se pueden añadir pequeñas cantidades de aditivos como TiO₂, Al₂O₃ o V₂O₃.
Procesado de MgO de gran pureza:
Para las aplicaciones que requieren cerámicas de MgO de gran pureza, no se pueden utilizar aditivos. En su lugar, se aplica un método de sinterización activada:
- El hidróxido de magnesio (Mg(OH)₂) se calcina a una temperatura adecuada para crear MgO activo con muchos defectos de red.
- A continuación, este MgO activo se sinteriza para producir cerámicas de óxido de magnesio de alto rendimiento.
Este método garantiza una pureza y un rendimiento excelentes, satisfaciendo las necesidades de las aplicaciones más exigentes.
Tabla de propiedades cerámicas de la magnesia (MgO)
Propiedad | Unidad | Valor |
Pureza | % | MgO :99.7% |
Color | blanco | |
Absorción de agua | % | 5.5 |
Densidad | cm³ | 3.4 |
Absorción de agua | g/% | 6.5 |
Resistencia a la flexión (MOR) (3 puntos) @ RT |
Mpa | 215 |
Term. Conductividad (400°C) | W/m-K | 44 |
CTE (20-1000°C) | 10-6/K-1 | 13 |
Temp. oper. máx. Temp. Aire | °C | 2200 |
Cont.Oper. Temp. Aire | °C | 1800 |
Capacidad calorífica específica | J/g-°C | 0.900 |
*Los valores representan las propiedades típicas de los materiales y pueden variar en función de la configuración del producto y del proceso de fabricación,
Para más información, no dude en Contacto.
Tipos comunes de materiales cerámicos de óxido de magnesio:
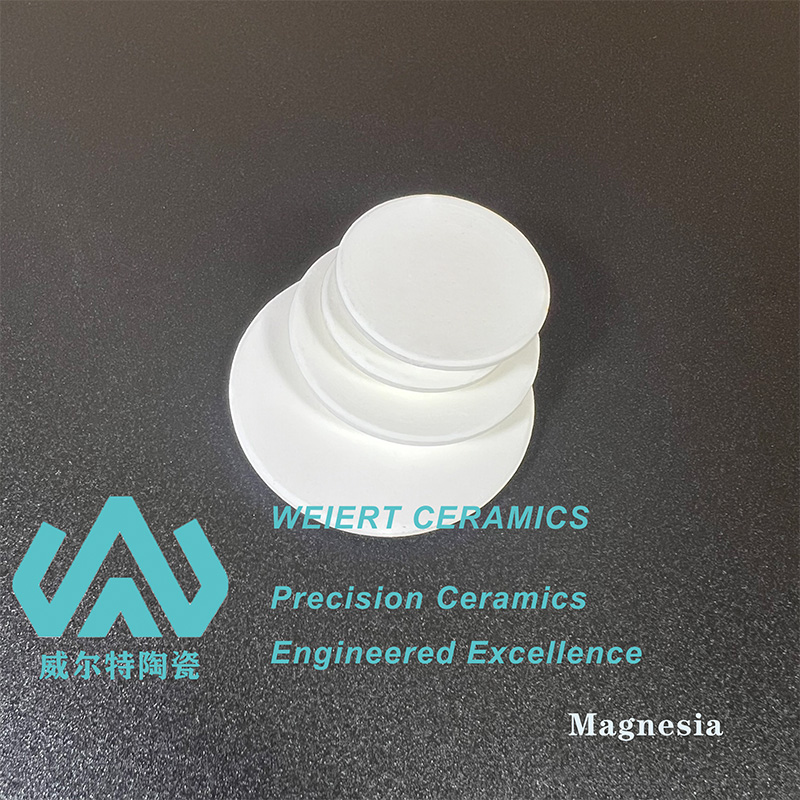
Magnesia MgO Cerámica
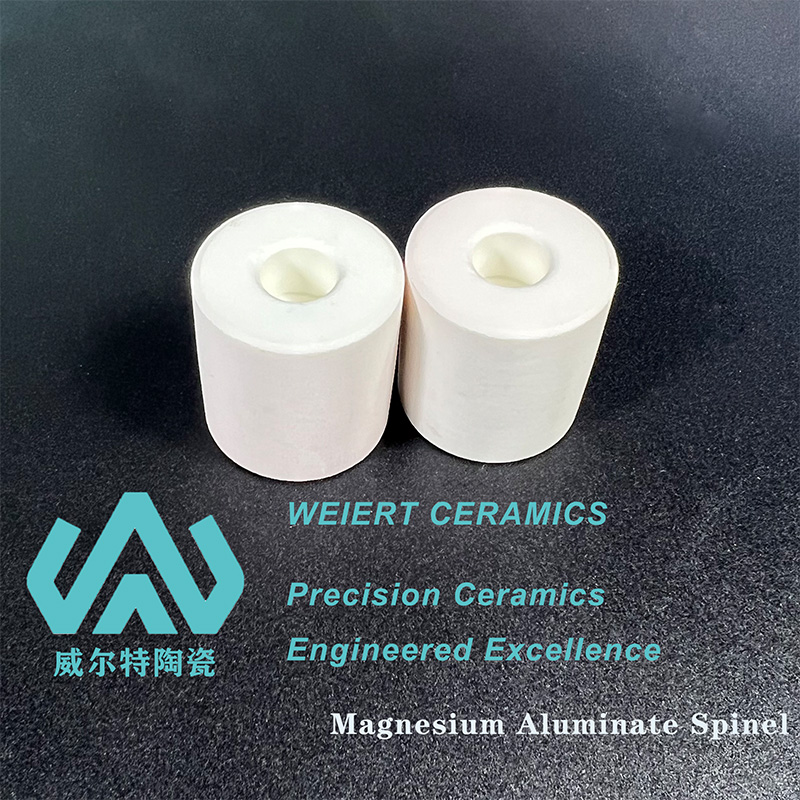
Espinela de aluminato de magnesio
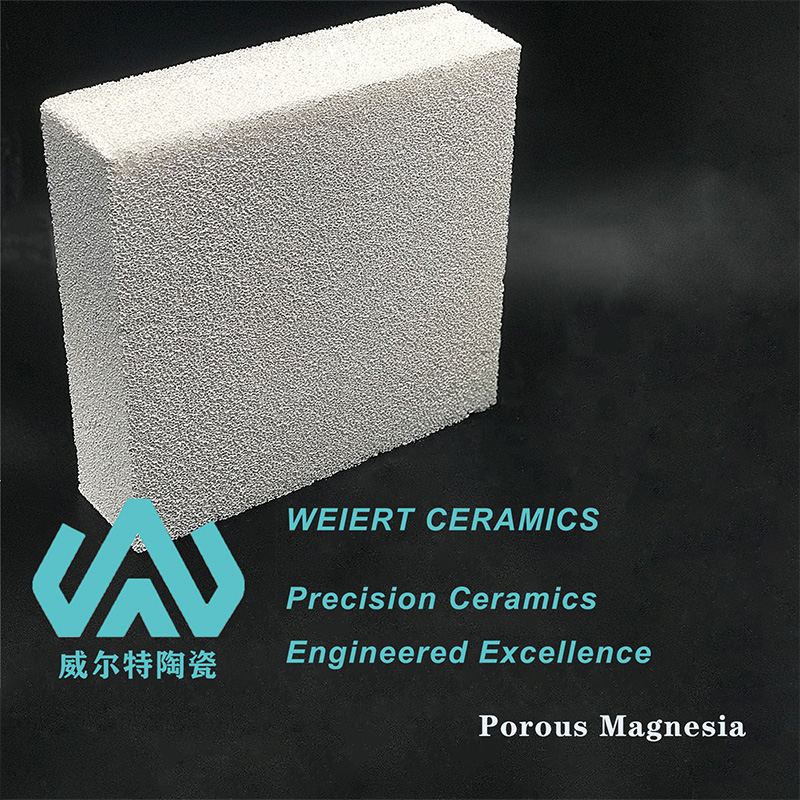
Cerámica porosa de magnesia
La cerámica de espinela de aluminato de magnesio, con la fórmula química MgAl₂O₄, es un material cerámico avanzado muy utilizado para crisoles. En comparación con la cerámica de magnesia (MgO), está co-sinterizada con 50%-70% Al₂O₃ y óxido de magnesio, dando lugar a una estructura densa y vitrificada. Esta composición proporciona una mayor resistencia al choque térmico, lo que la hace especialmente adecuada para fundir aleaciones de magnesio y otras aleaciones altamente reactivas.
En el pasado, los crisoles a base de hierro, como los de acero al carbono o acero inoxidable, se utilizaban habitualmente para la fundición de aleaciones de magnesio. Sin embargo, estos materiales son muy susceptibles a la corrosión por metales fundidos y fundentes, lo que reduce su vida útil. Además, el hierro contenido en los crisoles puede filtrarse a la aleación fundida y contaminarla. Los crisoles de grafito, aunque ofrecen una alta conductividad térmica, tienen una baja resistencia mecánica y son propensos a agrietarse en condiciones de calentamiento desiguales.
Las aleaciones de magnesio plantean retos únicos debido a su elevada presión de vapor (por ejemplo, 1037 Pa a 727°C). El magnesio fundido y sus vapores penetran fácilmente en los materiales cerámicos porosos, reaccionando con ellos y generando tensiones que provocan la degradación del material. Esto provoca daños estructurales, desprendimiento del material y contaminación de la aleación fundida.
Propiedades superiores de la cerámica de espinela de aluminato de magnesioLas aleaciones de magnesio presentan una alta reactividad química y pueden reaccionar con materiales cerámicos tradicionales como Al₂O₃, ZrO₂, SiC y SiO₂. Además, durante la fusión y el refinado, el magnesio reacciona fácilmente con el oxígeno, el nitrógeno y el vapor de agua, lo que provoca pérdidas por oxidación y subproductos residuales. Estas impurezas pueden afectar a la calidad y el rendimiento de los productos de aleación de magnesio. La cerámica de espinela de aluminato de magnesio (MgAl₂O₄) resuelve eficazmente estos problemas. Su densa microestructura y su superior resistencia a la oxidación impiden la infiltración de magnesio fundido y vapores. La adición de Al₂O₃ aumenta la densificación durante la sinterización, mejorando aún más su integridad estructural. Como resultado, este material es la opción preferida para procesar hierro de gran pureza y sus aleaciones, así como níquel, uranio, torio, zinc, estaño, aluminio y sus aleaciones.
WEIERT Ceramics Technology es el mejor fabricante de cerámica de espinela de aluminato de magnesio en China. No sólo somos productores de crisoles de espinela de aluminato de magnesio, sino que también ofrecemos servicios personalizados para productos cerámicos de espinela de aluminato de magnesio. No dude en ponerse en contacto con nosotros para cualquier consulta o requisito.
Las cerámicas porosas son materiales formados por sinterización de óxido de magnesio a altas temperaturas, lo que da lugar a una estructura con numerosos poros internos. Las cerámicas de magnesia porosa se producen utilizando óxido de magnesio de gran pureza con un contenido de magnesio superior a 95%. En cambio, las cerámicas de óxido de magnesio no porosas o densas (porosidad < 0,1%) suelen requerir la adición de otros componentes, y su contenido en magnesia suele oscilar entre 60-80%.
En función del tamaño de los poros, las cerámicas porosas de magnesia pueden clasificarse en microporos y macroporos. Los microporos son esenciales para los procesos de adsorción y purificación de gases o líquidos, incluida la purificación catalítica. Los macroporos, por su parte, desempeñan un papel fundamental en los sistemas de limpieza de filtros, el aislamiento térmico y las aplicaciones biomédicas.
The Applications of Magnesia Ceramic
Magnesia ceramics outperform alumina ceramics in both high-temperature stability and corrosion resistance. It has a wide range of applications, including:
Crisoles y refractarios: Se utiliza en las industrias de fundición de acero y vidrio, especialmente en condiciones corrosivas.
Procesamiento de metales: Adecuado para fundir metales y aleaciones, como aleaciones de níquel, aleaciones radiactivas de uranio y torio, y hierro y sus aleaciones.
Industria nuclear: Ideal para fundir uranio y torio de gran pureza en aplicaciones de energía atómica.
Tubos de protección de termopares: Proporciona protección térmica y química a los sensores.
Componentes electromagnéticos y ópticos: Se utiliza en cúpulas de radar y ventanas de proyección de radiación infrarroja debido a su capacidad para transmitir ondas electromagnéticas.
Soportes de sinterización: Serves as sintering carriers for ceramics, especially for processing corrosive and volatile substances like β-Al₂O₃ at high temperatures.
Materiales piezoeléctricos y superconductores: Actúa como materia prima para aplicaciones especializadas, ofreciendo propiedades como la resistencia a la corrosión del plomo y la no contaminación.
Why Choose WEIERT Ceramics?
WEIERT Ceramics Technology es la mejor empresa de cerámica MgO de China.
MgO ceramics’ combination of high-temperature performance, chemical stability, and corrosion resistance makes them indispensable for demanding industrial and scientific applications. We provide customized magnesia ceramic tubes, magnesia ceramic rings, magnesia blocks, and various complex magnesia ceramic components.